In this guide, discover our top three tips for successful ATEX product design
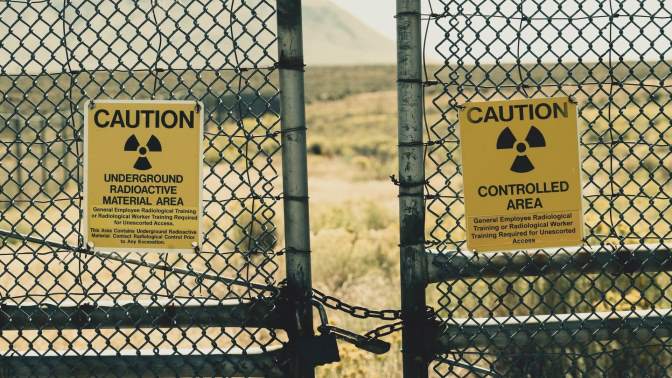
Flammable gases.
Vapours.
Mists.
Combustible dusts.
Any of these can cause an explosive atmosphere.
All that is required to trigger an explosion is:
- Enough of any flammable gas, vapour, mist, combustible dust
- Air
- A source of ignition
Explosions can result in death, serious injury and substantial damage.
Two of the most common ways of reducing the risk of explosions are:
- Preventing the release of hazardous substances, which can then result in explosive atmospheres
- Preventing sources of ignition
ATEX-designed equipment is developed to operate safely in an explosive atmosphere.
This guide will touch upon some terms and standards related to developing for explosive atmospheres before going into detail about how to approach ATEX product design for success.
Contents
- Terms & Standards around designing for explosive environments
- ATEX – what it is, its role in electronics product design
- ATEX Design – Your keys to successful product development
- The standards agency
- Highly specialised electronics design
- ATEX Design and the emergence of the hydrogen economy
- Main takeaways
Some terms and standards around designing for explosive environments
IS – Intrinsic Safety
IS is based around designing a circuit board, in order to prevent the board from causing an explosion through heat or sparking.
Intrinsically safe PCBs do not require an enclosure – in theory, you could put it uncased in a hazardous area – as the board is intrinsically designed to be safe.
EX – Explosion-proof Housing
EX is where you design a housing strong enough to contain an explosion, so that if there is a heat or ignition source within the box, it can’t cause an explosion which propagates outside of the box.
DSEAR – The Dangerous Substances and Explosive Atmospheres Regulations 2002
These guidelines require employers to eradicate or control the risks from explosive atmospheres in the workplace. A summary of DSEAR requirements can be found here.
IECEx
The International Electrotechnical Commission System for Certification to Standards Relating to Equipment for Use in Explosive Atmospheres.
One of the core aims of IECEx is to enable the international trade of equipment for use in potentially hazardous locations while maintaining the required level of safety.
When it comes to ATEX and IECEX certification for products, both processes require niche technical expertise and sufficient time to prepare, whether your are designing for Zone 2 or Zone 22.
The difference between IECEx and ATEX is that IECEx applies only to electrical equipment to be used in hazardous environments.
Whereas, ATEX applies to both electrical and non-electrical equipment.
In addition, IECEx also applies stricter criteria for evidence during the product certification process.
What is ATEX and why is it important in certain industries?
ATEX is the shortened version of ”Atmospheres Explosible” and relates to a set of European directives that regulate equipment and protective systems intended for use in potentially explosive atmospheres.
ATEX compliance, also known as control of explosive atmospheres, is crucial in industries like oil and gas, chemical, and mining in Europe and beyond to ensure safety by preventing the ignition of explosive gases or dust.
This is why obtaining ATEX approval for products in the form of gases, which involves testing for safe combustion, is essential for success in these industries, as required by the EU directive 94/9/EC, commonly known as the ATEX Directive, ATEX Equipment Directive and the ATEX Workplace Directive.
ATEX certificates are issued to equipment that has been tested and found to be compliant with the ATEX Directive, assuring that the equipment is safe for use in a particular zone within potentially explosive environments and that personnel are trained in the safe use of the equipment.
The equipment must also bear the CE marking, indicating that it meets the essential health and safety requirements set by the ATEX Directive and is approved for use in hazardous environments without the need for separate testing and documentation for each member state.
The Directives are:
This relates to equipment and protective systems intended for use in potentially explosive atmospheres.
This details the minimum requirements for improving the safety and health protection of workers potentially at risk from explosive atmospheres.
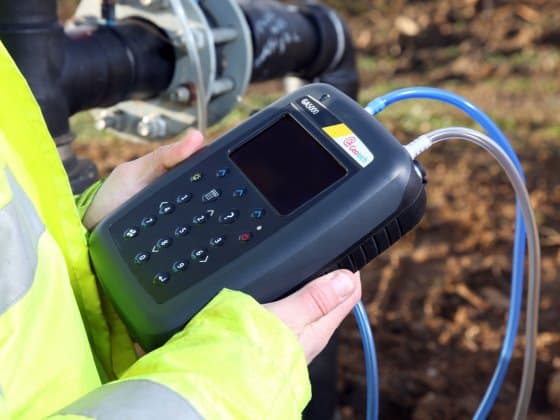
Effectively, with ATEX there are two things you try to avoid:
- sparking, and
- heat.
To avoid these, it is essential to do the correct calculations, printed circuit board layout, and schematic design, to solve both issues.
These calculations are central to the ATEX design process and intrinsic to working with the notified body required to sign off the design.
There will be times when you have to discuss with the notified body what the calculation methods are, as frequently calculations can be carried out in subtly different ways yielding different results.
On the software side, the focus is on low-power design, because a key element of intrinsically safe design is reducing the amount of power that the device uses.
Therefore, the real challenge in the art with intrinsically safe design is in keeping the power right down, whilst meeting the spec of the product doing what it needs to do and concurrently keeping within the standards on sparking and heat.
The other option for ATEX compliance is to use an explosion-proof container.
However, that can be very restrictive; explosion-proof containers aren’t suitable for many products, and you could also end up with a more expensive overall product if you go that route because the enclosure itself can be very costly.
Whereas, if you were to develop an intrinsically safe device, it doesn’t necessarily have to be that expensive a product at all, as intrinsic safety doesn’t imply expensive components per see.
ATEX Design – Your keys to successful product development
Our three keys to successful ATEX product design are:
- Keep ATEX front and centre of your development
- Be absolutely clear on standards
- Develop a good working relationship with the standards agency
Let’s go through each of these fundamentals in more detail…
Case study: Intrinsically safe gas analyser
1. Keep ATEX front & centre of your development
Don’t make the mistake of not thinking about ATEX until the end – i.e., completing your design and then deciding to “bolt on” ATEX functionality.
It must be considered at the planning stage. This principally refers to intrinsically safe design, rather than explosion-proof (referred to as EX.)
2. Be absolutely clear on standards
From the outset, you must know exactly which standards you need to meet. ATEX consists of several different classes and standards, with some harder than others.
Do not attempt to bite off more than you need to chew; avoid going for something harder than you need to achieve. Determine both your target gas group and zone before starting your design.
The gas group determines ignition temperatures, whilst the zoning governs the number of failure modes allowed and thus the redundancy of the protection elements.
As the ignition temperature of gases decreases, the task becomes rapidly more complex as the amount of power allowed onto the PCB also decreases.
Don’t over-engineer your design unnecessarily.
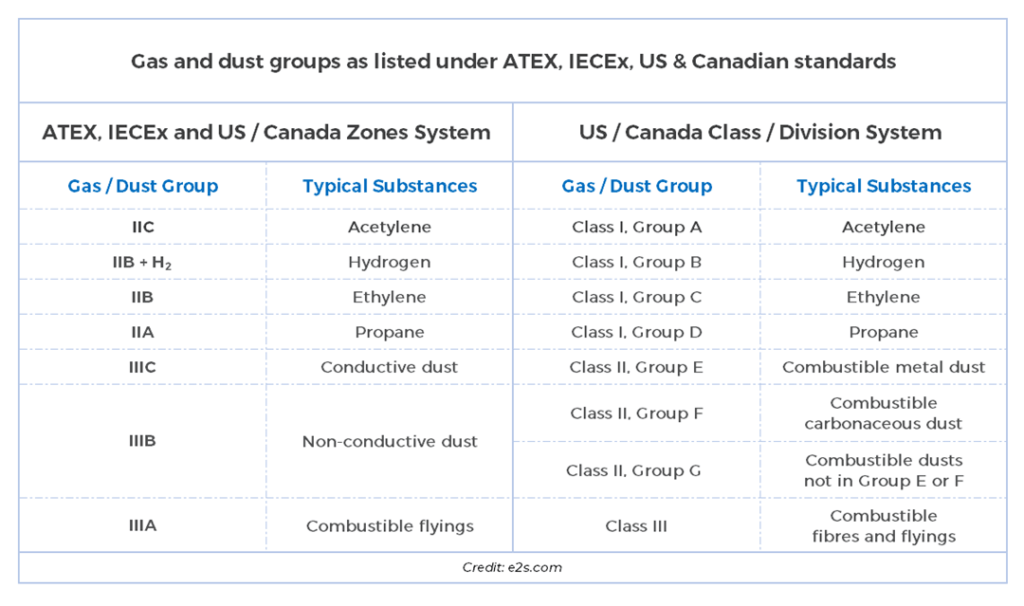
Temperature Classes
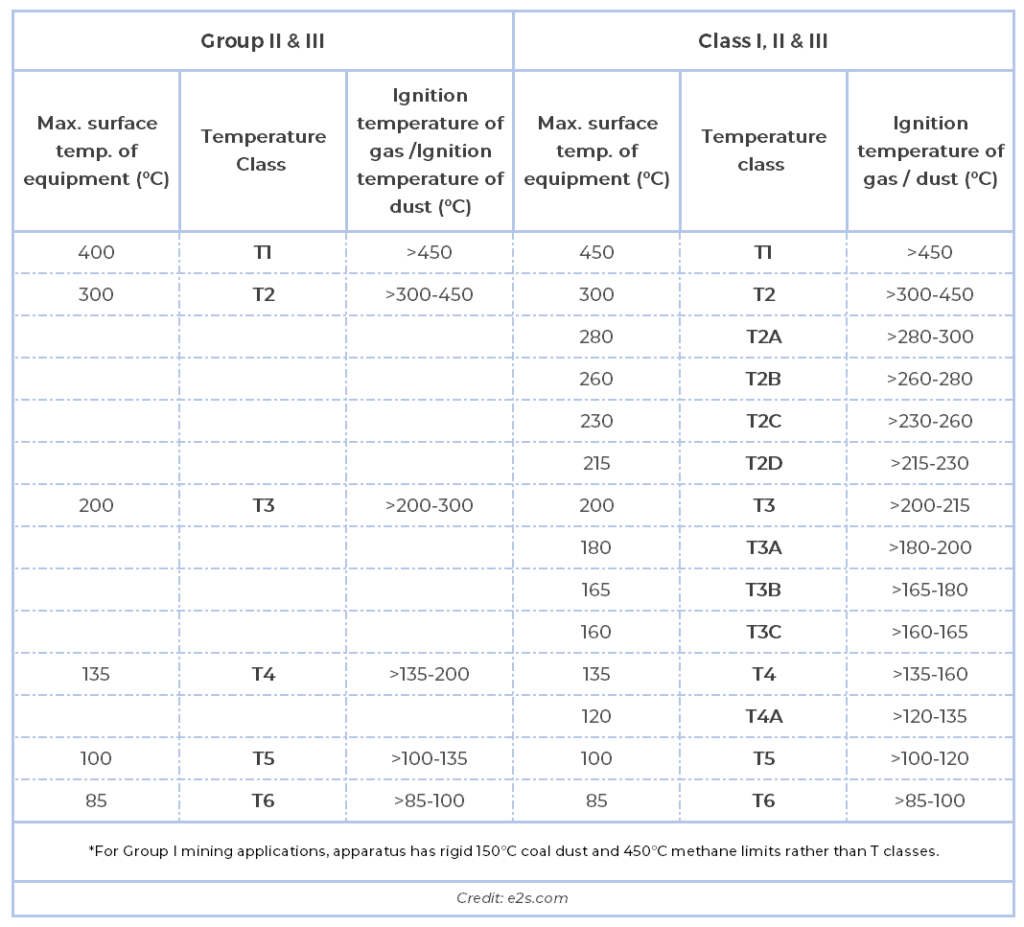
ATEX Certification – Classification (Hazardous Area Zones)
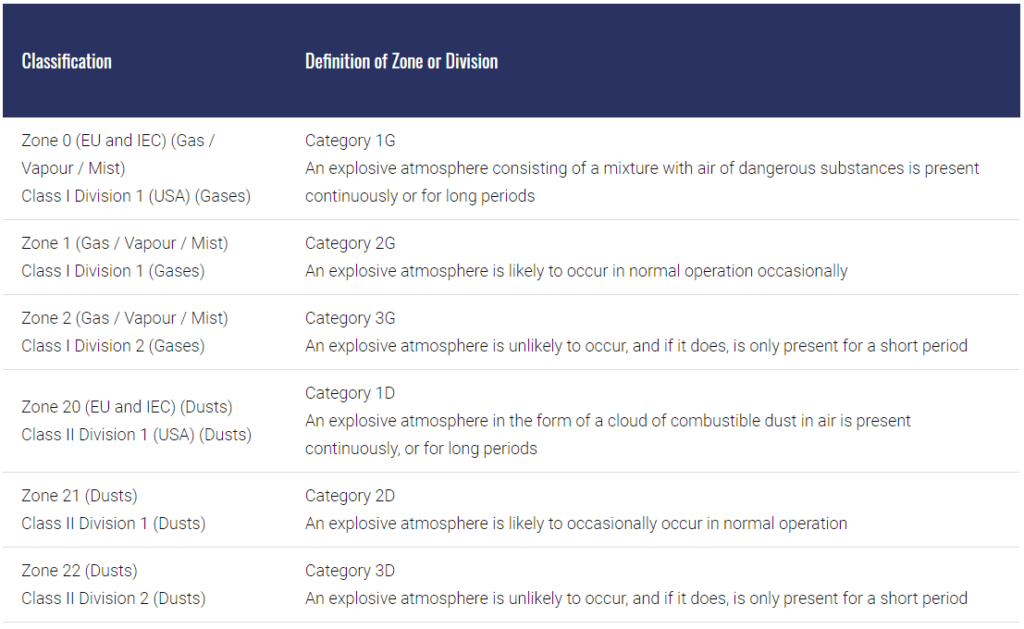
3. Develop a good working relationship with a standards agency
Work closely with a standards agency, perhaps on a consultancy basis.
There are many calculations involved in ATEX product development. Some of them are ambiguous as to how they’re done.
A good working relationship at project start will save you money later, when it comes to your full assessment.
The Standards Agency
As the examiners, the standards agency (i.e., notified body) – for example, one such as CSA Group – plays a crucial role in the development of ATEX-certified products.
If you’re not on board with them from the start, you risk failing the exam and missing out on certification.
With ATEX, you have to be certified by a notified body, rather than undertake a self-certification process, such as that for CE. It is essential to think the way the notified body thinks and do your calculations the way they do them.
It’s not always entirely clear how to do some of the calculations, because you’re dealing with a very complex set of regulations.
Sometimes, calculations can be made in more than one way, depending on the starting assumptions – not all of which will be in the standards.
Therefore, if they’re not done the way that the notified body expects, you could be entering a grey area – potentially costing you more project time.
In our experience at ByteSnap, when we found ourselves in that situation, we discussed it with the agency and managed to come to an agreement on the calculations.
Niche, complex electronics engineering
ATEX / EX / IS product design is a very niche and complex area of electronics engineering.
An interesting question is, in a world that’s moving away from fossil fuels to cleaner energy, how relevant is it?
One of the hottest topics in both the energy and green tech spaces currently is hydrogen.
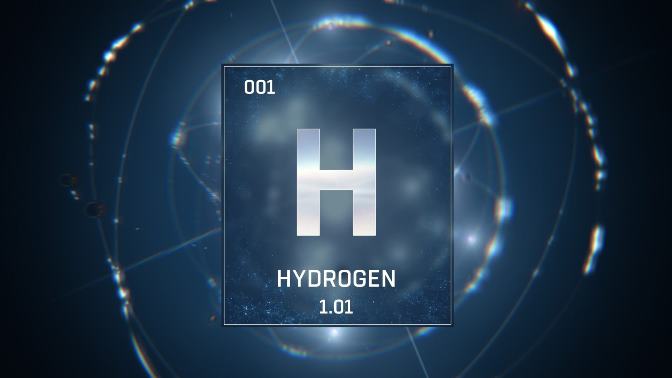
Hydrogen absolutely requires ATEX design. The Hydrogen Economy is set to be a key driver for ATEX in the future.
ATEX Design and the emergence of the hydrogen economy
Green tech is expanding by the minute with virtually everything going electric, but there’s lots of buzz – particularly in Japan, who are among the nations the way – in terms of hydrogen-powered vehicles (which is a whole other separate subject).
It has high energy density and has the potential to be very clean; hydrogen itself is clean – you burn hydrogen, you get water. Therefore, to many, it’s the perfect fuel.
The problem currently is that making hydrogen involves burning fossil fuels in general.
Over 90% of hydrogen today is made from coal, oil and natural gas.
The refining process, called reforming, separates hydrogen from carbon dioxide (CO2). However, that CO2 by product is often released into the atmosphere – thus contributing to global warming.
As such, even though you can make it from water and electricity, strictly speaking, it’s not really a clean fuel.
Nevertheless, with the rise of the new hydrogen economy, for example –
- wind-, solar-, or hydropower-generated green hydrogen being cited as a potentially viable energy source
- a new hydrogen working group set up by IECEx, the international standards body
- demand set to increase rapidly over the next few decades, according to analysts
– ATEX product design is very likely to grow in importance in the months and years ahead.
Main takeaways
1. This cannot be stressed enough – engaging with the standards agency at the start of your development really pays off.
Yes, it’s pricey as their hourly rates are expensive, but it’s money well spent because it means you are setting off in the right direction, and will end up with a product that passes. That’s probably the biggest takeaway.
2. Significant consideration and planning will be required for your development, much more so than for other types of electronic device, so remember to keep ATEX front and centre of your design project.
It will help you develop only what is strictly necessary to meet your spec and avoid unnecessary, costly over-engineering.
Excellence in ATEX design takes time
3. Also, it’s important to remember that it’s a slow design process. Designing an ATEX product isn’t something that’s fast or to be hurried.
Be realistic; don’t go into it expecting to get a product developed quickly in a few weeks; it’s very different from, say, consumer product design.
The difference is due to the extensive amounts of both calculations and checking.
There may be setbacks where you do things and they don’t work; you might not meet the power budgets at a particular point and so you have to go back. It is a time-intensive process.
On a more encouraging note, you can actually do much more within intrinsic safety – even within the power limits imposed by IS – because modern electronics have lower and lower power.
In years gone by, intrinsically safe design devices might have just been simple things like temperature sensors or pressure sensors.
Nowadays, due to mobile phones and other handheld devices with electronics needing lower power driving the semiconductor market, you can do more in the power budget you’re allowed.
Our latest intrinsically safe designs have DSP functionality, low-power radios and graphical user interfaces – something that would have been impossible decades ago.
Consequently, in the future, there’s potential for even more sophisticated, intrinsically safe products than there was in the past.
Outsourcing your ATEX product design project
Need support for your product development? ByteSnap’s engineers can assist your in-house team with all aspects of ATEX / IS device design.
ByteSnap has experience in developing end-to-end products designed for intrinsically safe gas areas.
Projects we have delivered include an explosive gas analyser, and a non-destructive testing system for installation in hazardous areas, right down to Zone 0.
Regarding the intricacies of this type of electronics design, ByteSnap has the in-house skills around schematic and PCB design to help you successfully complete your ATEX project on time and within budget.
As specialists in complex electronics and software, we have deep technical expertise in areas such as low-power radio and low-power design – staples of ATEX product development.
In addition, we are experienced in a particularly key part of this niche area of electronics design getting calculations through certification successfully.
Let's get started on your ATEX project
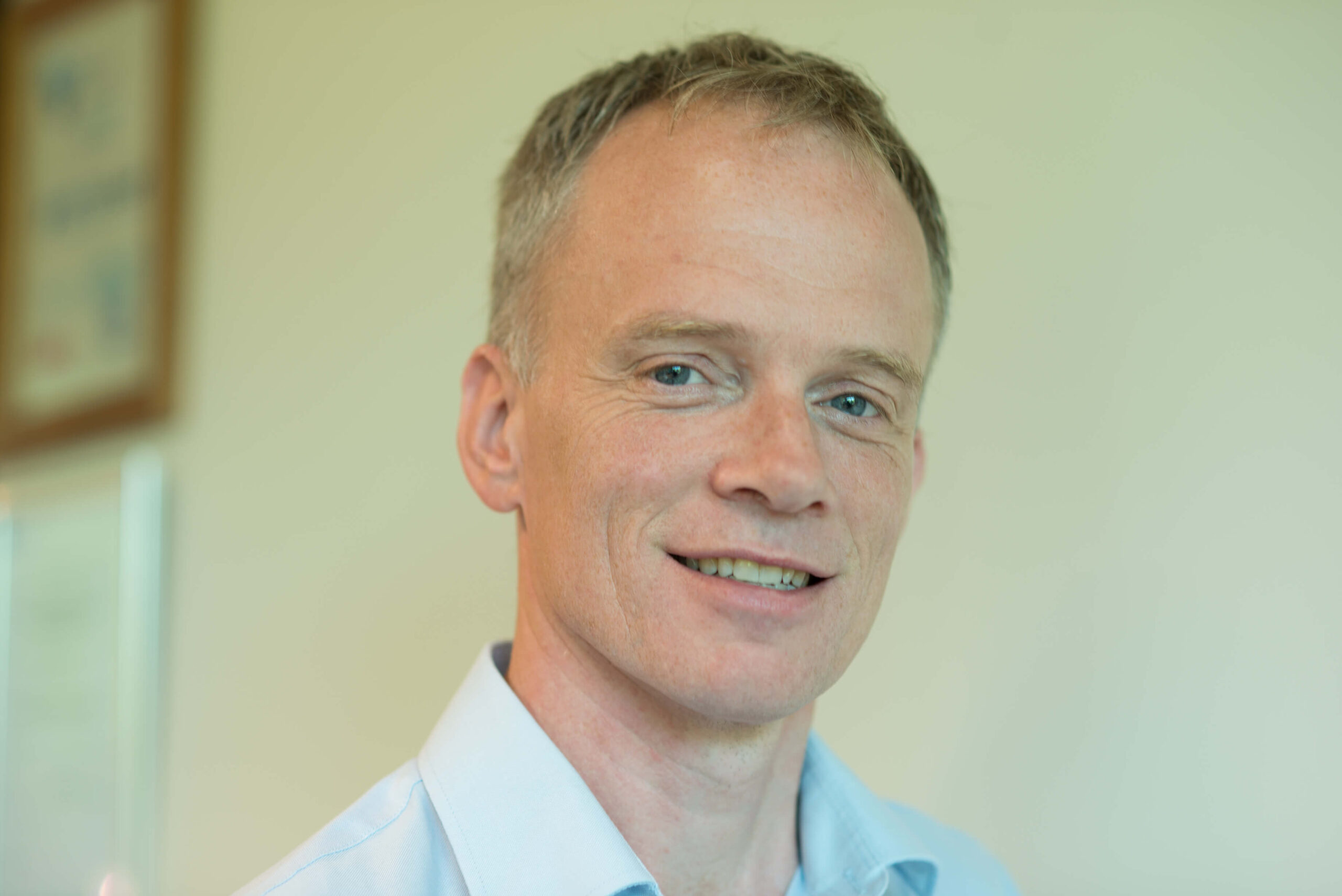
Dunstan is a chartered electronics engineer who has been providing embedded systems design, production and consultancy to businesses around the world for over 30 years.
Dunstan graduated from Cambridge University with a degree in electronics engineering in 1992. After working in the industry for several years, he co-founded multi-award-winning electronics engineering consultancy ByteSnap Design in 2008. He then went on to launch international EV charging design consultancy Versinetic during the 2020 global lockdown.
An experienced conference speaker domestically and internationally, Dunstan covers several areas of electronics product development, including IoT, integrated software design and complex project management.
In his spare time, Dunstan enjoys hiking and astronomy.