Production & PCBA Testing 101: Expert Tips for Success
When manufacturing costs can spiral into millions from a single undetected fault, comprehensive PCBA functional testing is more than just a quality control measure – it’s a critical business investment.
With electronic products becoming increasingly complex and time-to-market pressures mounting, manufacturers need testing solutions that deliver both thoroughness and efficiency.
At ByteSnap, we’ve helped countless companies overcome these challenges – saving one client from shipping 3,000 defective boards through our rigorous testing protocols.
In this comprehensive guide, we’ll walk you through our approach to custom PCBA functional testing, exploring the solutions that can protect your production line and your bottom line.
Contents
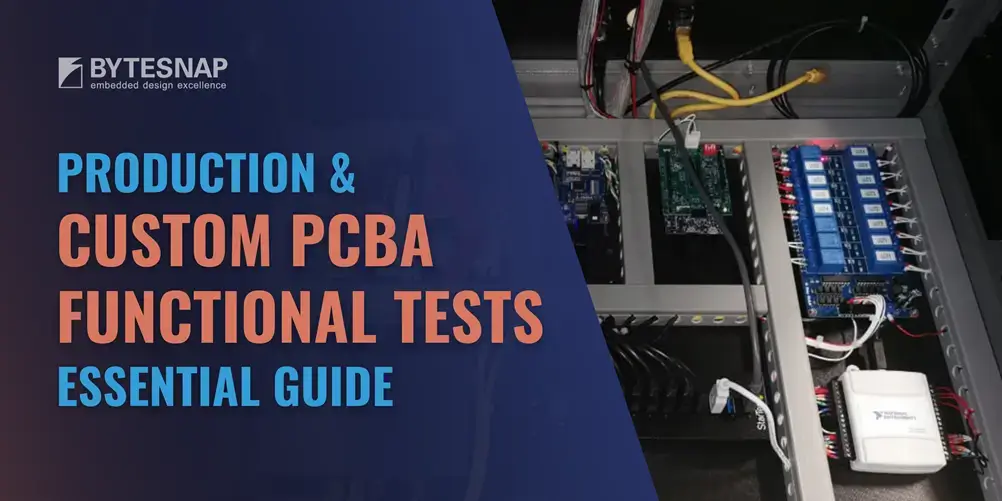
Every electronic printed circuit board design and its testing and programming requirements are unique.
At ByteSnap, we design bespoke functional test & programming turnkey solutions to meet the design requirements whilst using and incorporating recognised standard hardware.
Our solutions include:
1 - Automated "volume production" bed of nails programming and functional tests
This is a functional test solution that usually uses test points on the bottom of the PCBA in order to “functionally” test that the PCBA has been manufactured correctly to the engineering data.
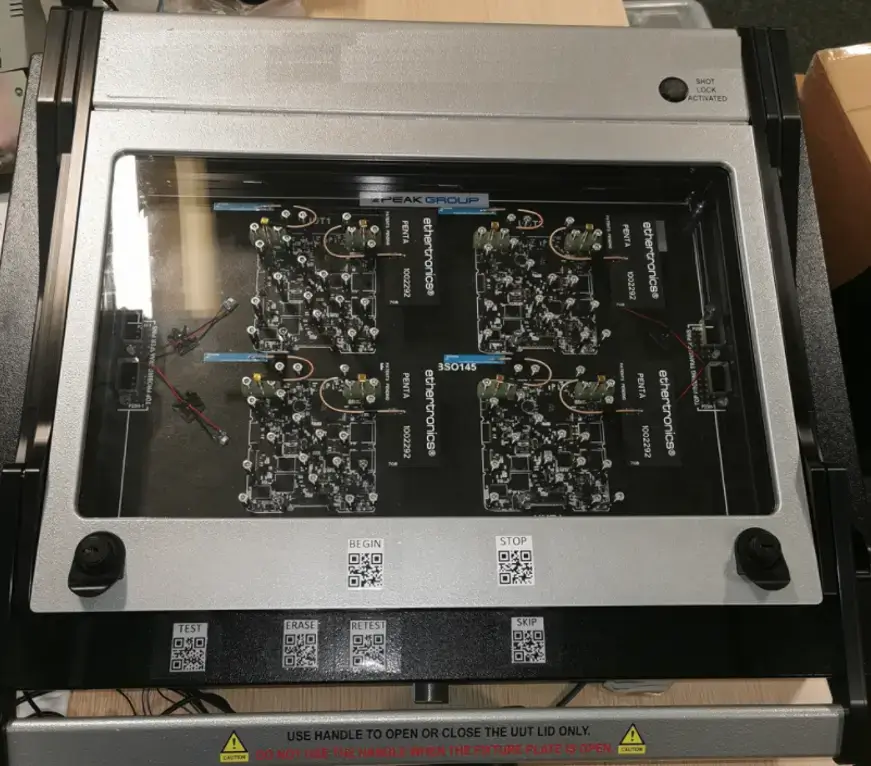
The solution is usually fully automated, can test several PCBA’s in parallel and also “bring up” and programme the PCBA with any required software.
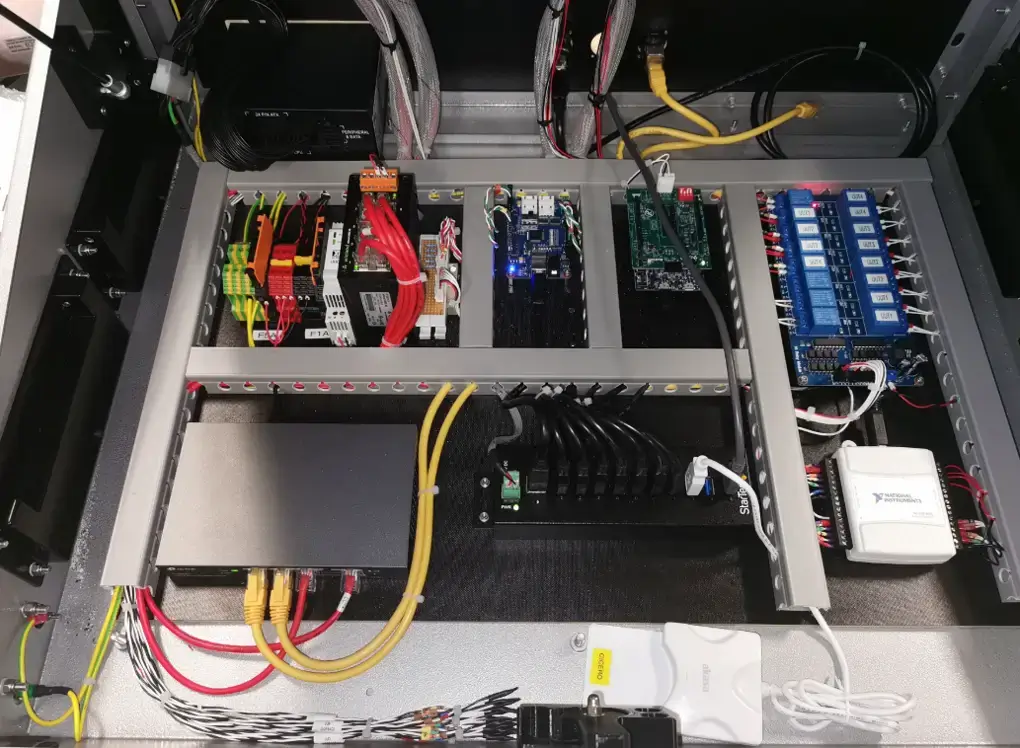
2 - Low volume bed of nails or bench type programming and functional tests
This is a functional test that usually uses test points on the bottom of the PCBA to “functionally” test that the PCBA has been manufactured correctly to the engineering data.
The solution can also “bring up” and programme the PCBA with any required software.
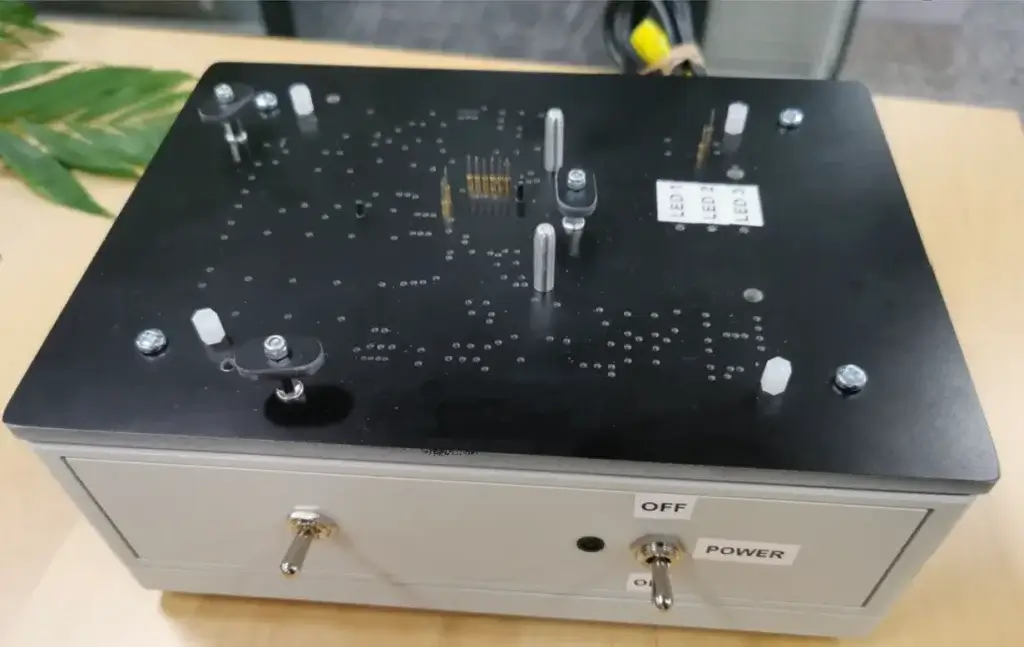
3 - Bespoke GUI test interfaces & options to connect test data to secure databases or other business systems (MRP)
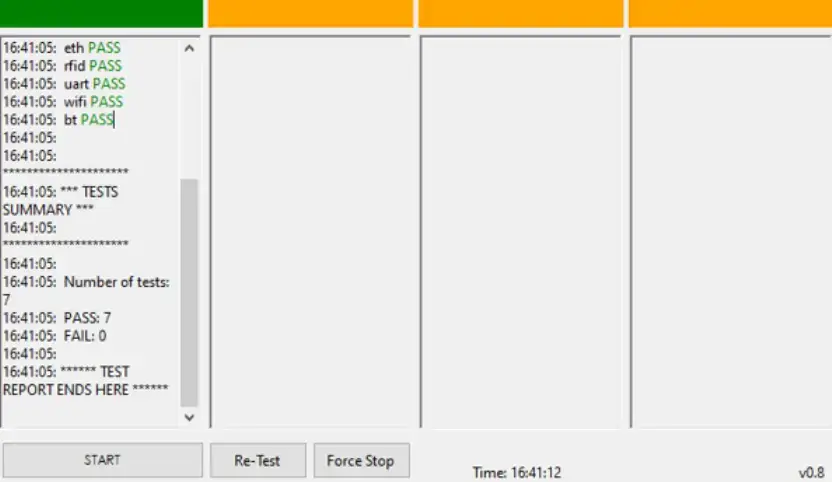
The test interface and data gathering solution is usually key in the functional test process.
This can be designed so that the operator requires very little understanding or knowledge to follow the on-screen instructions to carry out the functional test process, while test logs are written and maintained to a database or 3rd party application.
These custom solutions ensure comprehensive test and programming solutions while optimising for efficiency and cost-effectiveness.
Example: “3-up” Bed of Nails fixture - high level architecture
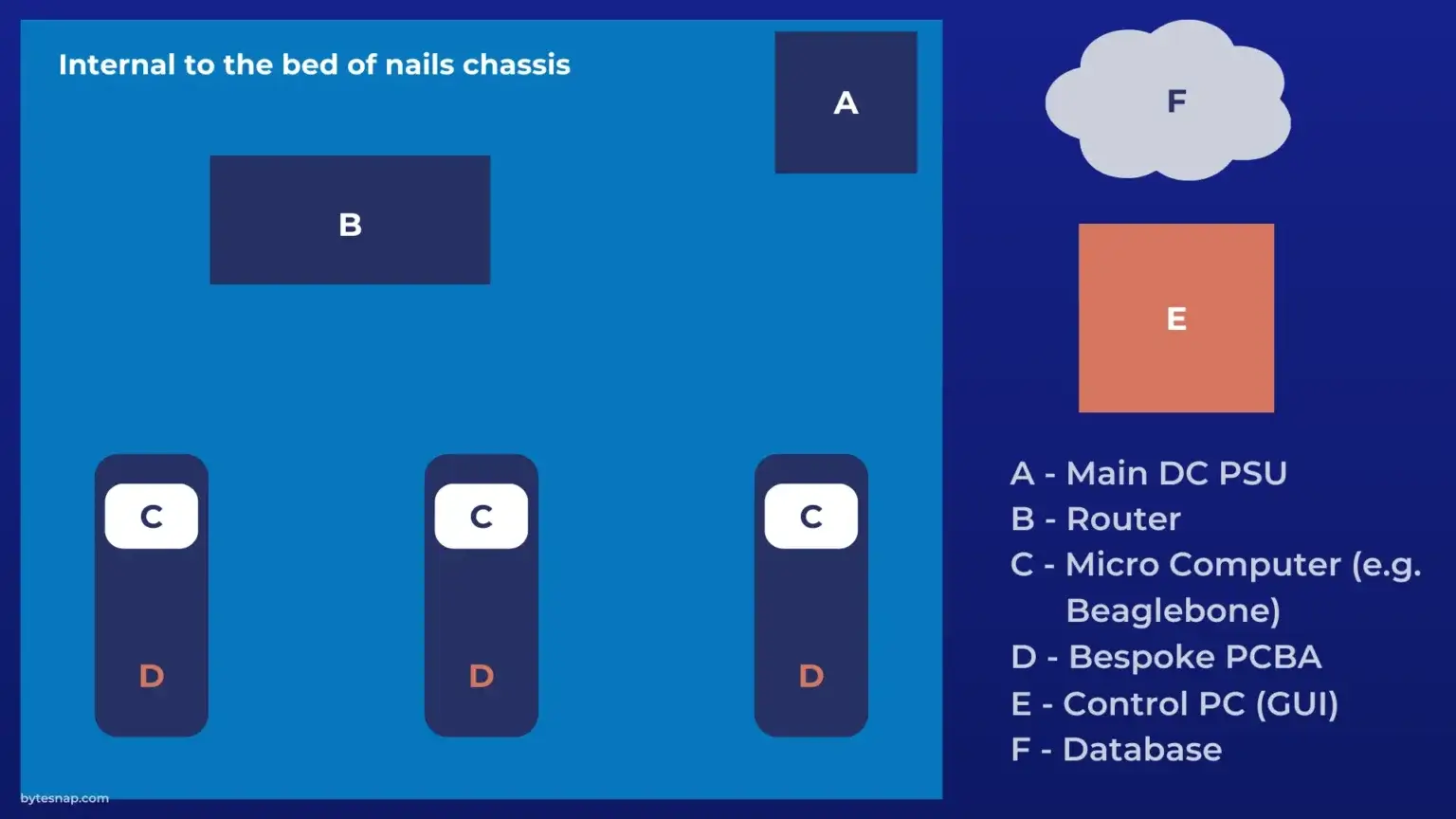
If we consider the high-level architecture design of a 3-up bed of nail style fixture internals:
A – DC rails for the internal fixture and *3 PCBA’s under test
B – Ethernet Data comms the 3 microcomputers and the control PC and database
C – An appropriate microcomputer (I.E Beaglebone/RPI…) This would be running bespoke mid-level code to control the on-board analogue and digital I/O which in turn is connected to “D” the test interface PCBA. This would communicate with the main test PC (GUI) for test control and also the database/cloud. This also manages programming of the PCBA under test.
D – Bespoke test PCBA, this has internal circuitry (sensors, DAQ’s, switching…) which in turns connects to the PCBA under test via the bed of nails pins.
E – Test PC to run the test control application, this may be a bespoke application again written in a mid-level language. This communicates directly with the microcomputers and required database or other third-party applications
F – Integration with an existing or bespoke database or third-party application (I.E MRP system)
Continuous Improvement and Evaluation
Our commitment to quality doesn’t end with the initial design and testing phase. We continuously evaluate and improve our processes. This includes:
- Regular design for test analysis services
- Recommendations and changes to PCB schematics and layouts to enhance testability
By staying vigilant and proactive, we help our clients avoid costly issues in production and in the field, ultimately saving them time and money while ensuring the highest product quality.
ByteSnap’s approach sets us apart in the industry. Our multi-functional team allows us to consider the bigger picture of manufacturing and testing from the outset. As well as meeting specifications, we’re focused on delivering a full turnkey solution that ensures quality manufacturing output.
This comprehensive approach helps our clients avoid costly pitfalls and ensures their products are not just functional, but exceptional.
The difference between testing a design and production test
A costly mistake in production testing is conflating design validation with manufacturing verification.
Some engineers implement expensive, complex tests to verify product specifications – a task that should have been completed during the development phase.
Production testing assumes that the design is correct; production testing checks that the manufactured products are identical to the designed “gold sample” product, which has been thoroughly design tested.
This puts creativity into the design of test rigs to make sure tests are fast and so cost-effective in production while still testing that the board is built correctly with in-spec components.
Impact of Comprehensive PCBA Functional Testing on Product Quality
Comprehensive electronic production testing has a profound impact on product quality and reliability. At ByteSnap, we’ve seen firsthand how higher test coverage directly correlates with better product performance and fewer field failures.
Our approach focuses on designing for test and manufacture from the ground up.
This strategy ensures that we can access necessary test points during production, implement a comprehensive testing strategy without compromising the product’s design, and prevent costly redesigns or manufacturing issues down the line.
A real-world example illustrates the critical importance of thorough testing.
In one project, our comprehensive test process identified an incorrect component with a part number very similar to the correct one. This discovery came after 3,000 boards had been produced. Thanks to our rigorous testing, this issue was quickly highlighted and prevented the shipment of potentially thousands of defective products.
Another case involved a performance test as part of an automated test process. While the product was passing the basic functional test, an issue was highlighted during a functional “performance test”. This led to the discovery of a batch issue with a certain component. Without this level of testing, a small percentage of final products would have failed in the field, potentially causing a high-cost product recall.
By implementing thorough testing processes, we help our clients avoid costly issues in production and also in the field, ultimately saving time and money while ensuring the highest product quality.
Tips for a Robust Electronic Production Testing Process
If you’re looking to improve your electronic production testing processes or seeking a partner for your product development and upcoming manufacturing process, consider these key points:
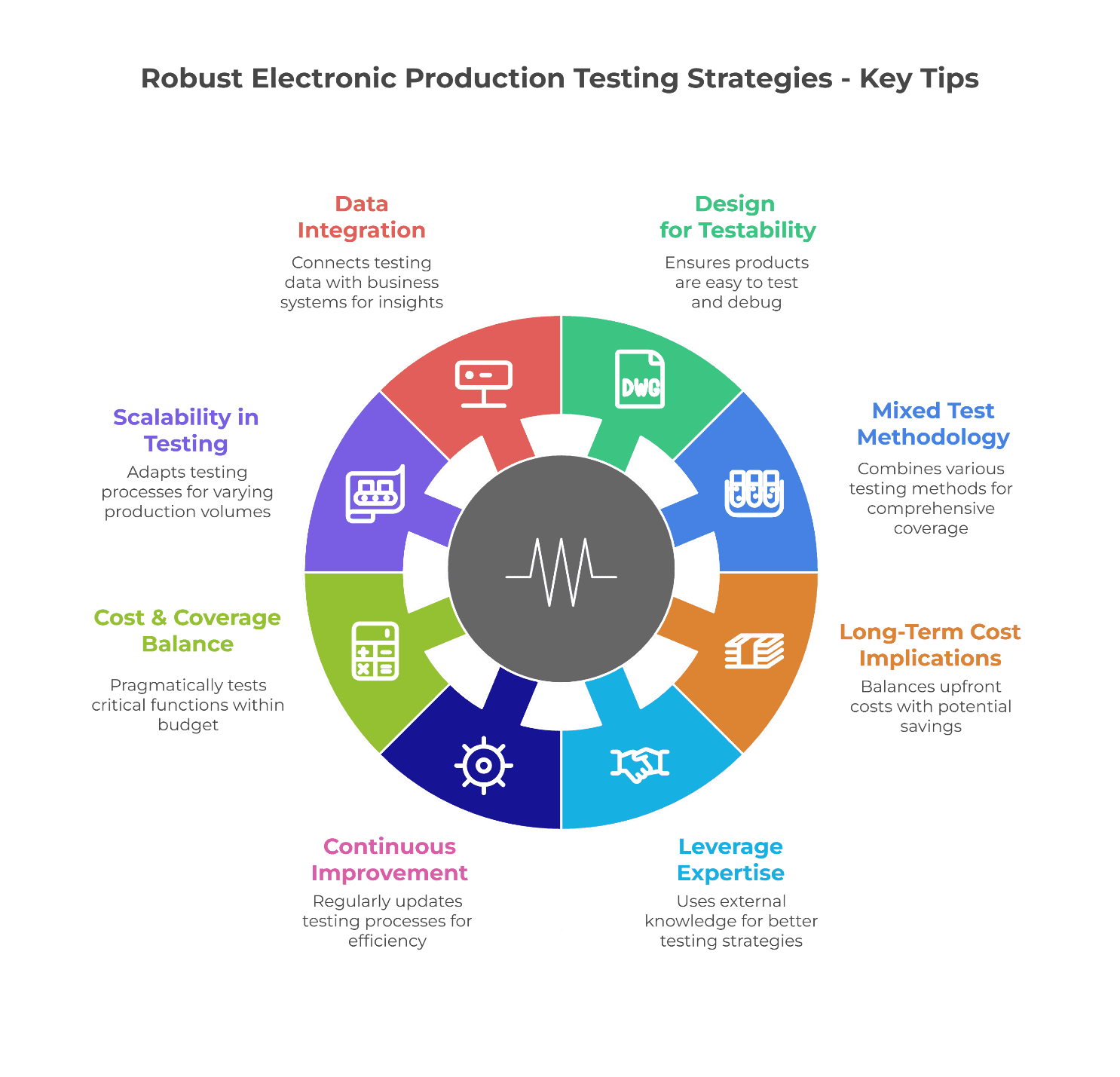
- Design for Test and Manufacture: Always keep in mind that your product needs to be not only functionally sound but also testable and manufacturable. Design with test points, debug headers, and other access features in mind.
- Implement a Mixed Test Methodology: Don’t rely on a single test approach. Combine methods like Automated Optical Inspection (AOI), boundary scan, functional testing, and final box testing to achieve 90-100% test coverage
- Consider the Long-Term Cost Implications: While comprehensive testing might seem costly upfront, it’s a fraction of potential losses from field failures or recalls. A small investment in testing can save millions in the long run
- Leverage Expertise: If you lack in-house experience, consider partnering with experts like ByteSnap. We can evaluate your design, suggest improvements for testability, and implement a robust test strategy
- Continuous Evaluation and Improvement: Regularly assess your testing processes and look for areas of improvement. As your products evolve, so should your testing strategies
- Balance Cost and Coverage: While aiming for 100% test coverage, be pragmatic. Assess the critical functions of your product and ensure these are thoroughly tested
- Design with Scalability in Mind: Your test process should be able to handle both low and high-volume production. Consider automated solutions that can scale with your production needs
- Data Integration: Look for opportunities to connect your test data to secure databases or other business systems (MRP). This integration can provide valuable insights and improve traceability
These tips can help you can significantly enhance your electronic production testing processes, leading to higher quality products, reduced field failures, and ultimately, a stronger bottom line.
Main Takeaways
Electronic production testing is a key process that should be integrated into every stage of product development.
As we’ve explored, comprehensive testing strategies are essential for ensuring electronic products’ quality, reliability, and success in today’s competitive market.
- Significantly reduce the risk of costly field failures and product recalls
- Enhance product quality and performance
- Improve customer satisfaction and brand reputation
- Achieve substantial cost savings in the long run
Remember, the goal is to strive for 90-100% test coverage using a mixed methodology.
This approach combines various testing techniques such as Automated Optical Inspection (AOI), In-Circuit Testing (ICT), programming and debugging, PCBA functional test and product test at the end of the line.
At ByteSnap, we understand that effective electronic production testing begins at the design stage. Our multi-functional team of hardware specialists, software engineers, and production test experts can provide a full turnkey solution, your products are designed for both manufacturability and testability from the ground up.
Don’t let testing be an afterthought. Make it an integral part of your product development process.
Production & Custom PCBA Functional Test Support
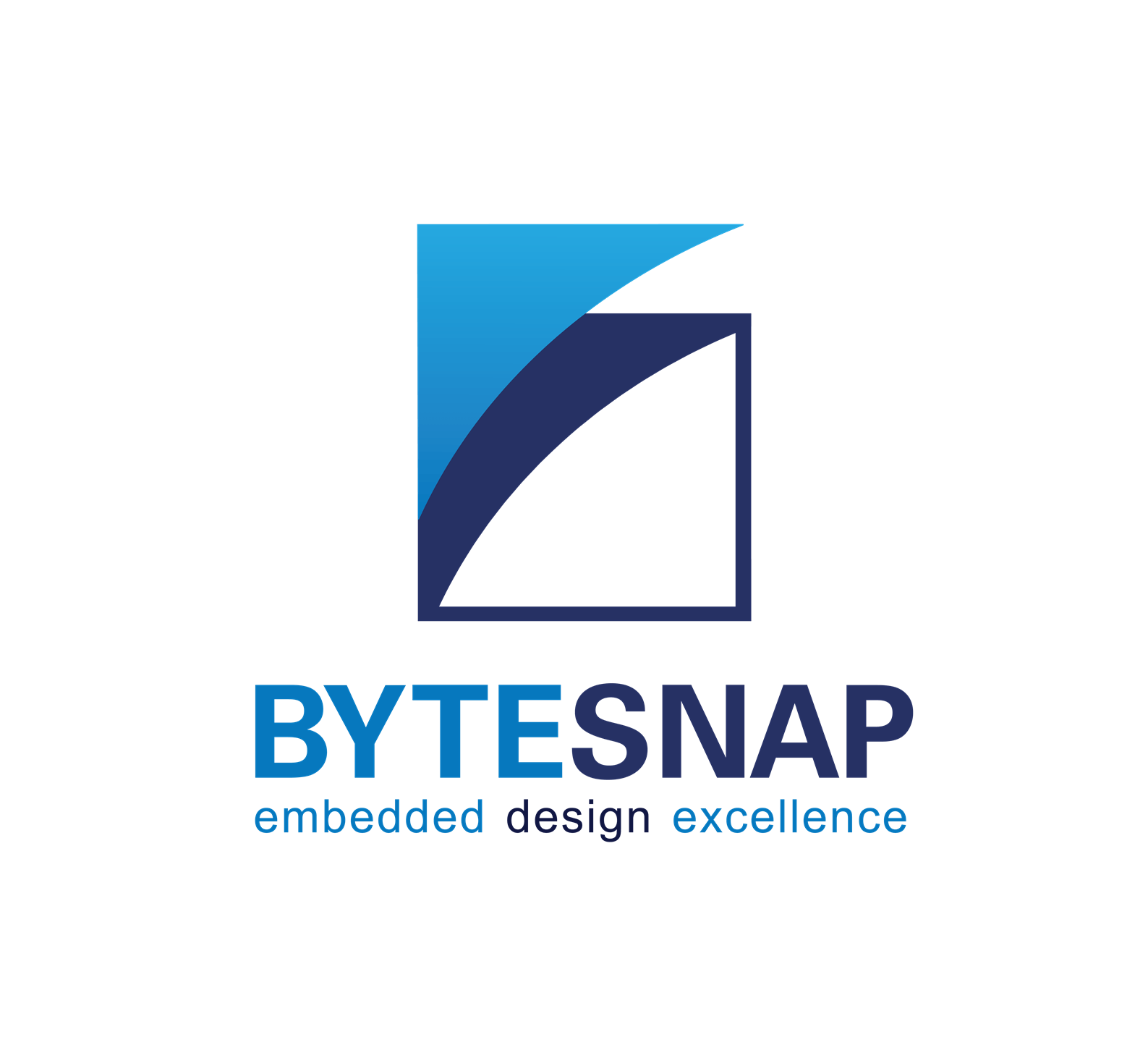
Founded in 2008, ByteSnap Design is an award-winning embedded systems design consultancy, offering a comprehensive range of services across the electronic product development lifecycle.
A highly skilled team of over 40 hardware and software engineers, our expertise spans several sectors, including IoT, automotive, industrial, medical, and consumer electronics.
The engineering consultants on the ByteSnap Editorial Team share their knowledge and practical tips to help you streamline your product development and accelerate designs to market successfully.
With their deep technical expertise and practical experience, they aim to provide valuable insights and actionable tips to guide you through the complex world of electronic product design and development, to help you bring innovative, reliable, and secure electronic products to market quickly and cost-effectively.