Working out the electronic design costs for your new product development takes in many phases. Read the guide to help you plan the costs of your next project.
Design & Development Pricing: How Much a New Electronic Design Project Costs
Before commissioning a new product development, it’s important that you establish a number of key project development essentials:
- Will the project technically work?
- Will it hit the required unit price?
- Will the delivery meet your timescale requirements?
- And – last but not least – what development budget is needed for the electronic product costs?
At ByteSnap, we engage in projects from a wide variety of markets and a wide variety of technical complexities. Every project is bespoke, so the cost question is not straightforward. However, here, we’ll try to give some pricing guidelines to explain what factors make up the price.
In this article, we’ll be covering “typical” projects. In the world of bespoke design, there are always outliers that sit outside of the boundaries discussed, but for the sake of offering guidance, think of this as meaning 80% of the projects that we encounter.
A development is broken into many phases. We’ll outline these with their associated costs in an approximate order that these stages take place.
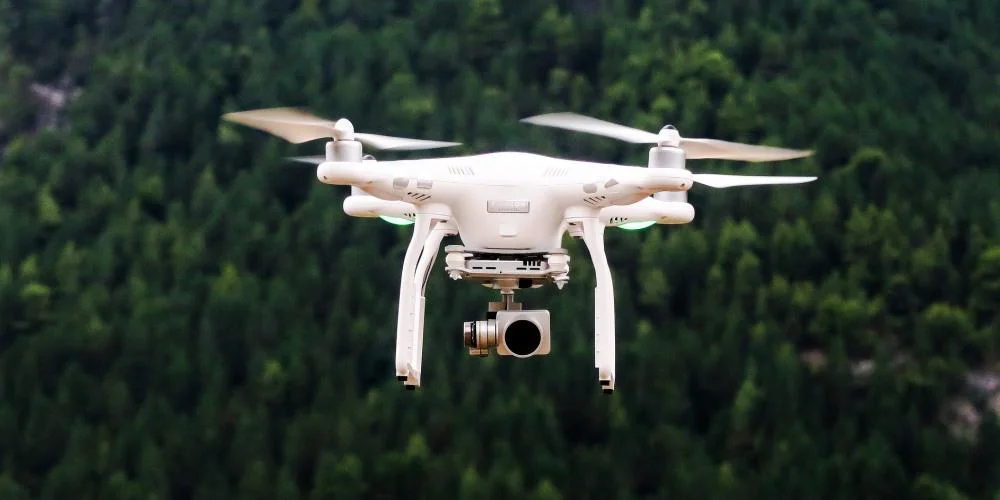
Electronic Design Costs For Each of the Development Stages:
Feasibility Study
For projects where the specification is undefined or there is a particular technical risk (e.g. radio range, BOM cost), we recommend a feasibility study stage to iron out these issues and to de-risk the remaining development. This study has no strings attached to continuing beyond the end – though we find in the majority of cases, our clients do.
Typical costs: £4,000 – £8,500+
Variables: What is being investigated, development kits or software tool fixed costs.
Find out more about ByteSnap’s Feasibility Study Service >>
Schematic and PCB development
Once the requirements specification is clearly defined and risks addressed, the hardware design begins. PCBs can range from a small board with a couple of chips on, to a large double sided, multi-layer PCB covered in high pin count devices (e.g. FPGAs).
PCB design costs vary with PCB density, as well as being related to the schematic design complexity. Packing electronics into a watch, for instance, might have 4x the PCB development budget required, versus the identical schematic design on an unconstrained rectangular board.
Typical costs: £10,000 – £60,000+
Variables: The size and complexity of the design, reuse of existing IP, PCB density.
Find out more about ByteSnap’s Electronic Board Design Service >>
FPGA
Large FPGA projects have their own set of project stages (e.g. planning, rtl, testbench, timing closure) and can be man years of development time. However, for the purposes of this article, we’re excluding ASIC prototyping and instead referring to FPGAs used within a system for things such as image signal processing functions integrating IP blocks with custom written code.
Typical costs: £10,000-£60,000+
Variables: The size and complexity of the design, use of third-party IP and their licensing costs, if any.
Find out more about ByteSnap’s FPGA Development Service >>
Prototype production
Typical costs: £1,500 – £6,000+ for a small set (3-5) of prototypes on 20 days turnaround. Most projects, other than the simplest, would require 2-3 prototype production runs.
Variables: Number of prototypes, turnaround time (costs can increase dramatically for turnarounds under 4 weeks), number of production runs.
Test
The electronics hardware is tested before being handed over to a software engineer, assuming that the board isn’t purely analogue. This also includes the hardware engineer’s time supporting the software development and investigating any issues.
Typical costs: £5,000 – £30,000+
Variables: The size and complexity of the design, reuse of existing IP, PCB density.
Industrial Design
ByteSnap Design works with a number of industrial design partners where our customers do not carry out the design themselves. The designers will generate concept designs for the customer to choose from until a final design is chosen. The industrial design for manufacture then follows.
Typical costs: £10,000 – £40,000+
Variables: Complexity and aesthetics of the design
Compliance testing
Often the forgotten sting-in-the-tail of the design process. To sell a product in any jurisdiction requires testing to published standards. For each geography, a different set of standards may apply, requiring a new set of tests.
Typical costs: £5,000 – £30,000+ per region
Variables: Standards required e.g. EMC, radio, safety, environmental; complexity of device – in particular, the number of interface cables associated with it.
Tooling costs for enclosure manufacture
Most electronic products are housed in injection moulded enclosures. A tool is custom made to mould the cases and the cost of this tool is generally the most substantial single investment in the process.
Typical costs: £10,000 – £80,000+
Variables: Size of the tool, number of parts, level of detail required
Manufacturing Setup
There are costs associated with sub-contract manufacturing setup. These include programming robots, test software and test jigs.
Typical costs: £1,000 – £10,000+
Variables: Complexity of test, type of test methodology, such as functional test only, JTAG or bed-of-nails. Often, a mixture of these is used.
Find out more about ByteSnap’s Manufacturing Support Service >>
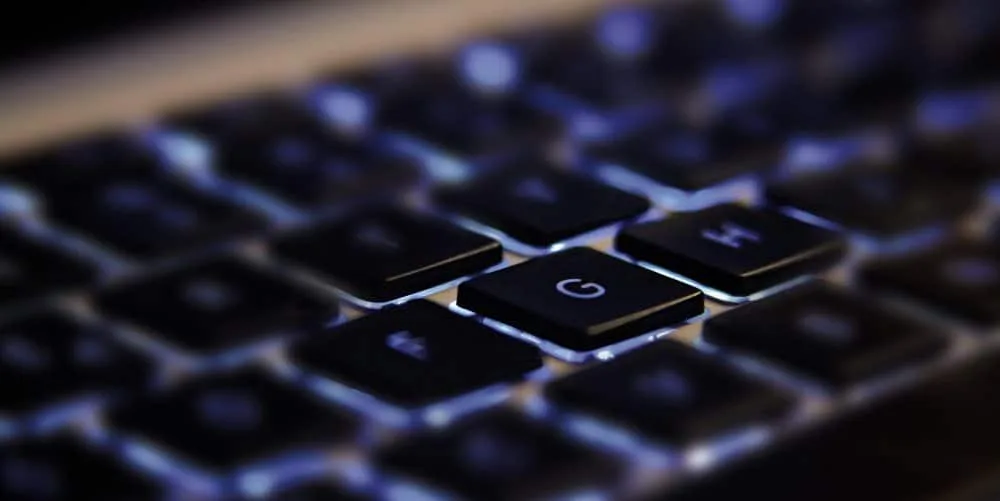
Electronic Design Costs for the Software Development Stages:
Android and iPhone Applications
Applications for phones range enormously from simple apps that just show web pages, through to complex 3D gaming applications. For the purpose of this article we are talking about industrial, IoT or logistics type apps. Mobile platform development can be costed using the following:
- The development of the application: £5000-£80000+
This is broken into:
- Setup and initial configuration
- Functional background tasks
- Each screen exposed to the user
- Generally, simpler screens like Splash, Settings, About, Configuration, etc.; around £500 – £1,000+ per screen to implement
- There could be a main or hub screen that is complex, has lots of user interaction, contains sophisticated logic behind the scenes. Guide cost for this, £1,000 – £4,000+
- Testing
- Unit testing – testing each item individually
- System testing – testing many functions all operating as a whole
- Stress testing – testing one or more items under heavy load
- Longevity testing – testing the app over a period of time
- Unit testing is required for any release. The others can be performed either by you or our engineering consultants – but they should be done for any reliable product
- Release
- App store registration through Apple or for Android
- Multiple platforms
- Effort to write the application for multiple devices (Samsung S9 and A70) or multiple platforms (Apple/Android) will require different programming languages, different tools and more testing on the multiple devices:
- Simple single platform application – generally £10,000 – £15,000
- Simple multiple platform application – £15,000 – £20,000
- More complex multiple platform application – probably between £30,000 and £60,000+. You could expect this to include:
- A web enabled application (AWS/Azure)
- A high level of security, uses HTTPS, local encryption, pin/biometric input
- A well-polished user interface experience
- Testing
- Release to App stores (Android/iOS)
- 7-10 UI screens to the user
- Code written in a cross-platform development tool, such as Flutter or Xamarin
Find out more about ByteSnap’s Industrial Android Application Development Service >>
Find out more about ByteSnap’s Industrial iPhone Application Development Service >>
Embedded Software & Electronic Design Costs
This is an application on the embedded hardware that has a single or main purpose. It is the core logic that ties the OS and hardware together into what is the product.
Applications are normally either headless, in which case they don’t have a screen or other visual output (like a Wi-Fi router), or they are UI driven with an LCD or other display output. Usually, these will have a touch screen or button input as well, such as a kiosk or point of sale device.
Applications are normally as sophisticated as the hardware they are required to run on.
For instance, if the product has 10 different chips to support the main CPU – say Bluetooth, Wi-Fi, Accelerometer, LCD, Touch, Buttons, 3G, Light sensor, Camera, Battery – then it will require a more intricate application than a simpler physical device with just a GPS.
The time estimated for the hardware development can often give an indication of the time that will be required for the application. Although the ratio can vary a huge amount, 2-4x is typical. For example, if you have an expectation of £40,000 for the hardware, you could be looking at a budget of £80,000 to £160,000 on top for the embedded software development. This isn’t always the case – it can be lower and higher – however, that 2-4x formula is generally a good rule of thumb.
Board Support Packages & Electronic Design Costs
Board support packages (BSPs) are the configuration and drivers that are used for the low-level hardware interaction. This is the same for Linux or Windows Embedded. For Android, it is more complex as this is a Java platform on top of Linux – therefore, you have drivers and configuration, and then further configuration of this.
BSPs, like the embedded software, are as multifaceted as the hardware they run on. For every hardware input/output/function, there needs to be a hardware driver and also the configuration of that driver. The starting point of any hardware design should consider the availability of up-to-date drivers. Writing drivers from scratch is a last resort; in many cases it is both easier and cheaper to change the hardware to accommodate missing drivers.
Available drivers may require configuration, modification and testing. Some drivers will work out of the box on your new hardware, others may require minimal work. Then, there will be drivers that may require weeks of effort if they deviate from the tested reference platform in some way. It isn’t always easy to tell; configuration of CPUs is so extensive that manufacturers normally release software tested in a small number of ways. This leaves many available configurations untested or unsupported in software. Deviation from the reference board will incur risk of the software needing more and more modifications and extensions to fix issues untested by the majority of users.
Design of hardware using modules (CPU+RAM+Flash etc. on a single PCB) can cut down the development risk. Usually, this means using the supplied Wi-Fi/BT, network chips, RAM, Flash, RTC and other peripherals, but it can be too prescriptive sometimes for some. Requirements may dictate their hardware (such as size, power, temperature), or it can be too expensive for high volume runs, with the module cost being more than just the sum of the parts they make up.
As a rule of thumb, the hardware design effort mirrors that of the BSP configuration, driver development or adaptation and BSP testing. You should generally expect to budget the same effort for the hardware development of a ‘chip down’ design for the BSP, or anywhere from 50-100% of the hardware design effort for a SOM or module design.
Example: for a £30,000 hardware based on a SOM module, it may be another £30,000+ for the BSP effort.
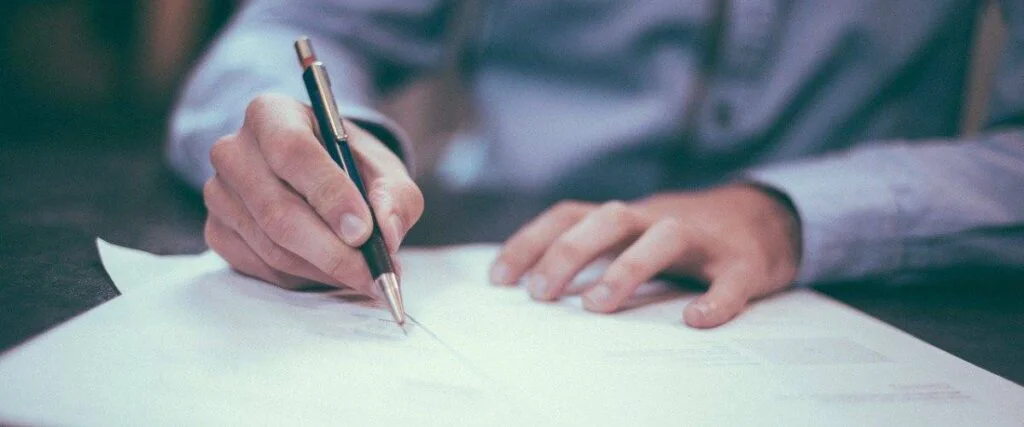
Types of Contract:
Broadly speaking, design consultancies offer two types of commercial contract – each with their own advantages and disadvantages.
Time and Materials
This is the simpler contract type. You pay for hours booked to the project as they are used. Time is tracking in a time-sheet system, allowing complete visibility of where time is spent and by whom. Normally, an estimate will be given which will be worked against, where there is a Statement of Work (SoW) to quote against.
Where used
- Design Rescue
- Picking up work from a 3rd party
- Application software, particularly involving GUIs
- Statement of Work is not clearly defined
- High level of risk
- Small jobs (e.g. less than 2 weeks)
Advantages
- Highly flexible
- If a project comes in under budget, you save money
- The only option where there isn’t a defined Statement of Work and acceptance criteria, or where a project is being picked up part way through from another developer (e.g. our Design Rescue Service)
Disadvantages
- The end budget is not guaranteed at the outset
- No warranty, as all work is chargeable
Fixed Cost
Where there is a well-defined Statement of Work, a fixed price may be offered.
Where used
- Well defined Statement of Work and specification
- Project time > 2 weeks (approx.)
- Well defined feasibility studies
Advantages
- Your budget is known at the start of the project assuming there are no specification changes
- Work has a warranty attached for a specified time period
Disadvantages
- Specification changes may incur requests for more budget – this very much depends on the timing of the change (e.g. the earlier the better) and the complexity it implies
- If a project comes in under budget, you are still tied to the agreed fixed cost
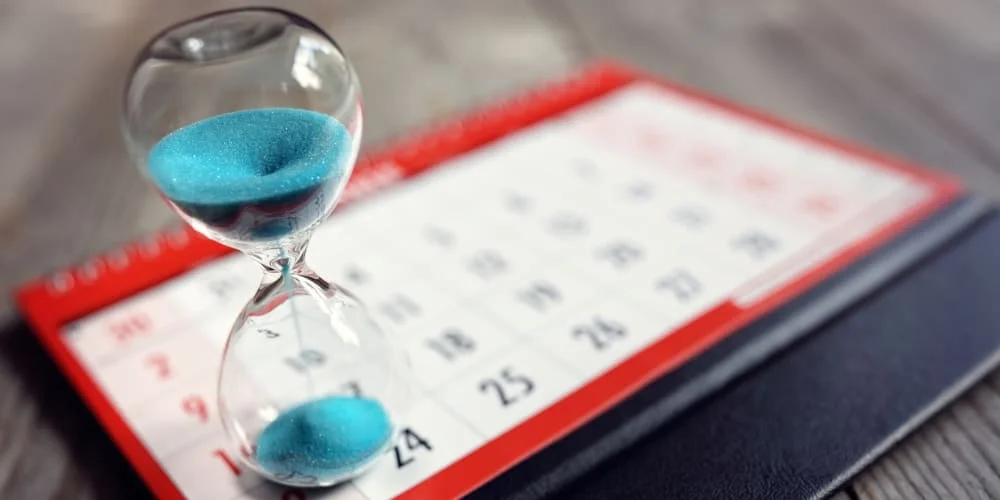
Time: Electronic Design Costs
Fundamentally, the cost of a project is heavily correlated with the number of man hours required to complete the work. With a single engineer on the job, the number of man hours also correlates with the elapsed duration of the project, whilst with a larger team, this is not so much the case.
Therefore, at its most basic, the development cost formula is simply:
Cost per hour x Number of hours
For this reason, hourly rates are often focussed upon at an early stage. However, this is hugely misleading, as the experience of the engineer and their access to pre-existing IP that can be leveraged on a project means that the number of hours is a big variable between competing development teams.
We have seen many examples of outsourced development firms claiming a $10 per hour cost, then producing uncompetitive quotes due to the number of engineering hours that they then assign to each task.
Characteristically, hourly rates for engineers in consulting firms can range from £100 – £200+ depending on the size of firm, experience and how niche the work is. Smaller, one or two-man bands may charge out at less than this, whilst global firms can be higher.
Conclusion
Now, you have some insight into what goes into budgeting for the development of an electronic design product. Costs can vary widely in bringing a device or system to life and to market, with factors outlined here influencing the final sum. The foundations to successful electronic product design lie in technical prowess, realistic expectations, and meticulous planning, research and budgeting.
Ensure that your foundations are in place well before embarking on your product development journey.
We’ve used our expertise to put together a handy guide for the cost to design and develop a new electronics product.
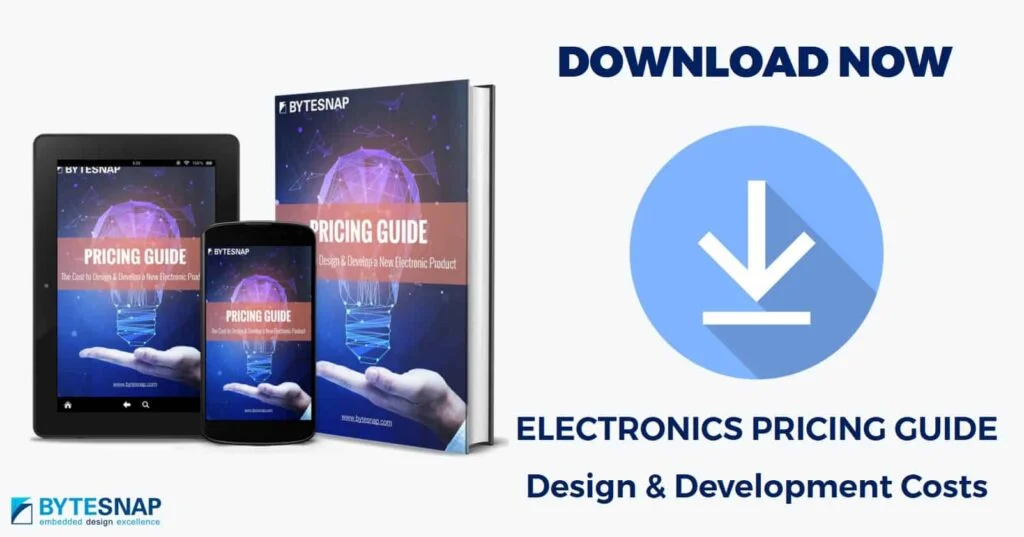
How can ByteSnap help you today?
From start-ups to blue chips, ByteSnap’s electronic design engineers are enabling companies to stay a step ahead by providing them with bespoke solutions. Maintain your competitive edge – contact us today and let your business be among them!